Professor Martin Jackson
MEng PhD DIC
School of Chemical, Materials and Biological Engineering
Professor of Advanced Metals Processing

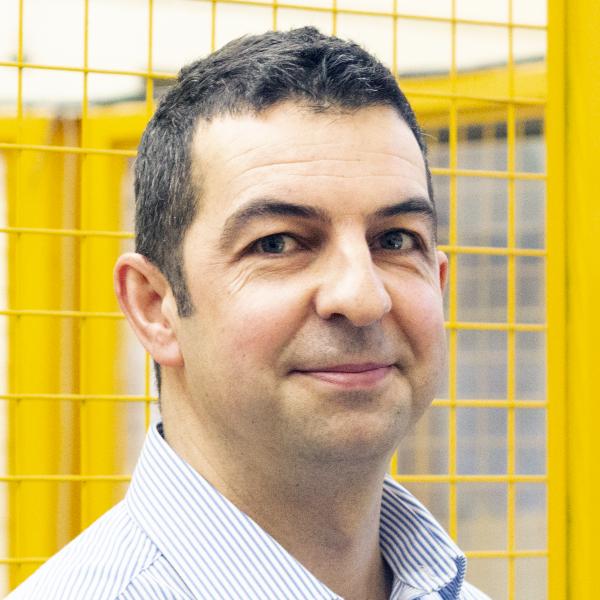
Full contact details
School of Chemical, Materials and Biological Engineering
Sir Robert Hadfield Building
Mappin Street
葫芦影业
S1 3JD
- Profile
-
After obtaining an M.Eng (First) from 葫芦影业, I initially followed an aerospace materials career working for Rolls-Royce before studying for a PhD at Imperial College London 鈥 "predicting microstructural evolution during forging of Ti alloys (EPSRC/QinetiQ)".
Between 2001 and 2005 I worked as a Research Associate and Lecturer at Imperial on a range of Conform, hot rolling and forging projects for the UK and US defence sectors. In 2005 I was awarded a Royal Academy of Engineering/EPSRC Research Fellowship with a remit 鈥渢o develop solid-state processes to reduce the cost of titanium鈥 and moved back to the department in 2008. I was appointed to Professor of Advanced Metals Processing in 2019. Director of Aerospace Engineering (2015-2019), Royce Research Area Lead for Advanced Metals Processing (2019-2024). Since 2015 I have represented the UK at the World Titanium Committee. (Chair of Ti-2023 in Edinburgh). I have been a member of the IOM3 Non-ferrous & Light Metals Committee for over 20 years. I have a HVM Catapult Researcher in Residence position at NMIS/AFRC (University of Strathclyde). I am the principal contact for the DSTL DMEx platform and Principal Scientist for their Land Working Group.
- Research interests
-
My research group focus on working 100% with industry (currently automotive, aerospace, sports goods and defence) to reduce cost in solid-state processes (forging -> machining), this includes creating digital fingerprints of microstructure through machining force response analysis. This includes working alongside machine tool manufacturers. We are pioneers in the recycling of aerospace machining swarf / powder: utilising Conform (continuous extrusion) to create wire/springs and field-assisted sintering technology (FAST/SPS) to produce near-net shapes with as-forged properties (FAST-forge). We also produce new higher performance titanium alloys for the aerospace sector. We have generated a number of patents with industry partners.
Key research interests:
- New disruptive in-process NDE technique: digital microstructures directly from machining force response.
- Machine tool insert degradation mechanisms during machining of titanium and nickel superalloys.
- Microstructure and Property prediction (digital twins) during solid-state processing (forging, rolling and extrusion).
- Recycling of aerospace waste streams (swarf and AM powder) using Conform [continuous extrusion] and field-assisted sintering technology [FAST].
- Creator of new opportunities for sustainable processing. From powder/swarf to product in two steps: FAST-forge, CIP-FAST, AddFAST, FAST-roll and FAST-form
- Publications
-
Journal articles
Chapters
Conference proceedings papers
Theses / Dissertations
Preprints
- Research group
-
- Teaching interests
-
Having worked in - and carried out metallurgy research with - the aerospace industry for 20 years, My expertise and teaching centres around the metallurgy of advanced light alloys and associated manufacturing for the aerospace and automotive sectors, with module structures that aim to provide engineering students with applied industrial experience of metals manufacturing.
I have written three book chapters on titanium alloys for both undergraduates and postgraduates studying the disciplines of aerospace, materials and automotive engineering.
- Teaching activities
-
AER61005 Industrial training Programme in Aerospace Materials (with Rolls-Royce)
MAT3333/333/AER330 Light Alloys
- Professional activities and memberships
-
IOM3 Non-ferrous & Light Alloys