Charging towards the next generation of batteries
Batteries are everywhere, but the process for manufacturing them is expensive, energy intensive and relies on depleting resources. Our researchers are at the forefront of developing new, innovative materials to create a brighter future for batteries.
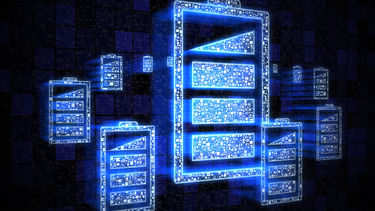
While we may not give them a second thought, from mobile phones and laptops to remote controls and smoke alarms, batteries are everywhere and power most of our everyday devices.
With every use, batteries gradually deteriorate until they can no longer store enough power. With household items, this usually brings a moment of frustration and a drop-off to the local battery recycling point. But tackling the longevity and disposal of larger-scale batteries such as those found in electric vehicles isn’t as simple.
Electric vehicles are gaining popularity, with data from the Society of Motor Manufacturers and Traders showing that 1.1 million electric cars are now on UK roads, a rise of more than 50 per cent over the past year. Although these vehicles produce next to no emissions while driving, the production of their batteries in particular still has a significant environmental impact due to the amount of energy required for the procurement of raw materials and the manufacturing process itself.
The UK Government has a legally binding target of net-zero carbon emissions by 2050. It is expected that the design, development, manufacturing and recycling of batteries will play a fundamental role in reaching this target. But to improve the performance of existing materials within batteries and to develop new materials that are more effective, it is vital to understand the foundation of how efficient battery materials operate.
Collaborating with industry and academic partners, researchers at ºù«Ӱҵ are reducing the carbon footprint of making the materials found in batteries and finding alternatives to the expensive and non-abundant materials the world currently depends on to make them. Working towards this shared goal, Dr Innes McClelland designed a cell to provide valuable insight into how materials inside batteries react during operation.
Understanding batteries
Lithium-ion batteries, such as those found in your phone, laptop and electric toothbrush, are rechargeable and have been in widespread use since the 1990s.
Like other batteries, a lithium-ion battery is made of power-storing compartments called cells. Each cell has three components: a positive electrode known as a cathode (shown on the + terminal) typically made of lithium and a mix of elements such as cobalt, nickel and iron, a negative electrode known as an anode (shown on the - terminal) and an electrolyte that connects them, allowing the transfer of lithium ions but not electrons.
When the battery is charging, lithium ions, or molecules with a positive electrical charge, move from the cathode to the anode. When the battery is being used, or discharging, the ions move from the anode back to the cathode.
However, even though lithium-ion batteries have a long-lasting life when compared to standard batteries, their performance and effectiveness fluctuate and gradually decline over time. This is due to the materials used inside, which have a high capacity, but often suffer an irreversible loss of power from the first charge. These materials discharge and undergo gradual degradation processes over extended operation.
ºù«Ӱҵ’s breakthrough
To design new and improved alternatives to lithium-ion batteries, it is important to first fully understand how the transmission of lithium ions works.
Previous experiments in this area relied on methods that studied the overall performance of components found within the battery but lacked the insight of how materials themselves behave internally. During his PhD at the University of ºù«Ӱҵ, Dr Innes McClelland designed a cell that would do just that.
In collaboration with his co-supervisor Dr Peter Baker and engineers from ISIS Neutron and Muon Source, his supervisor Professor Serena Cussen at the University of ºù«Ӱҵ and colleagues from the Faraday Institution next-generation cathode project FutureCat, he was able to design a cell that measures the lithium diffusion within the battery at over 70 points during the first cycle.
Using Innes’ new cell, the group were able to investigate what might be causing the lithium diffusion to never restore to its original state. showed that the slow diffusion was due to the surface of the cathode, and that focussing on stabilising this surface would create more opportunities for successfully improving the properties and performance of the battery.
This exciting development opens up a wide range of opportunities for further battery research as it provides a unique perspective of the diffusion of ions from inside the materials themselves whilst in operation. Working with the through a Facility Development studentship, which supported Dr Innes McClelland for his PhD, this project was awarded the .
Findings from research such as Innes’ work are then shared with industry and academic institutions to propel the UK to the forefront of the global lithium ion battery market.
Our work starts very much at the start of the food chain for battery research. We focus on understanding and dissecting small-scale batteries to understand how they can be improved. We then feed this knowledge into industry who apply it to larger-scale batteries such as electric car battery packs which can weigh well over 500kg
Dr Innes McClelland
Department of Materials Science and Engineering
Working with industry
was established in 2017 to put the UK at the forefront of the development, manufacture and production of electrical storage technologies such as lithium-ion batteries.
Based within the institution, is a project set out to develop cathode materials to drive the transition towards electric vehicles. Led by Professor Serena Cussen from the University of ºù«Ӱҵ and Professor Louis Piper from the University of Warwick, the team of researchers, scientists and engineers are spread out across seven universities and collaborate with UK-based industry partners and the Science and Technology Facilities Council.
The collaborative project brings together expertise from fields such as chemistry, physics, materials science and engineering, to merge perspectives on developing the next generation of cathode materials. They are also joined by industry partners from across the battery supply chain, as well as partners at the ISIS Neutron and Muon Facility and the National Physical Laboratory.
The quickening pace of climate change is accelerating the need for cheaper, safer, and environmentally friendly batteries. Collaborative projects such as FutureCat are crucial for moving technology forward and placing the UK at the forefront of innovative electrical storage technologies.
Written by Alina Moore