Manufacturing and Structural Integrity
Our Manufacturing and Structural Integrity group delivers research across a wide range of sectors, often through multi-disciplinary activities.
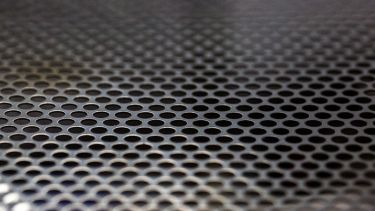
Overview
Research in the Manufacturing area focuses on developing advanced manufacturing technologies specialising in subtractive and additive manufacturing, polymers, composites, and flexible metal forming technologies. Our expertise ranges from materials selection to machining and the effect of manufacturing processes on functional performance. The research spans a wide range of technology readiness levels (TRL) from fundamental to applied research. This includes several collaborations with the University's multi-million-pound Advanced Manufacturing Research Centre.
Research in the Structural Integrity area covers a wide range of engineering applications and addresses industrial problems concerned with the performance of materials during manufacturing and the fatigue and fracture of components in service. State-of-the-art testing facilities and characterisation techniques (eg full-field strain and temperature measurements, high-resolution computed tomography-based damage quantification) are combined with advanced modelling techniques to predict the deformation and failure of a wide range of materials by considering the effect of both microstructure and manufacturing processes.
Our academics have expertise in a number of disciplines, including mechanical engineering, manufacturing engineering, materials science and engineering, ergonomics and chemistry, and engage in research with experts from fields as diverse as biomechanics, psychology and biology.
Research centres/capabilities
Polymer and Composite Engineering Centre (PCEC)
The Polymer and Composite Engineering Centre is a state-of-the-art research centre dedicated to innovation in the science of polymers and composite materials.
ºù«Ӱҵ Tomography Centre (STC)
The ºù«Ӱҵ Tomography Centre provides access and expertise to high resolution cutting edge tomography equipment with thermo-mechanical and electro-chemical stages for in-situ and in-operando 3D characterisation of materials.
Advanced Polymer Sintering Laboratory (APSL)
Research within the APSL is focused around powdered-polymer Additive Manufacturing (3D Printing), and in particular the Laser Sintering and High Speed Sintering processes. A large area of our research is around developing our understanding of the ways in which materials interact with the processes themselves, and how we can use this knowledge to improve the quality of the parts and components they produce. We work a lot with industry, for example helping companies to understand more about 3D Printing, in order to help them develop better, more advanced, materials.
Our experts
Facilities
To foster productive collaborations, our state-of-the-art equipment is based across a number of labs, with complementary facilities and expertise from other disciplines.
For example, our metal additive manufacturing work is primarily conducted with colleagues from our Department of Materials Science and Engineering, while our polymer additive manufacturing facilities are co-located with the University's composites labs. Examples of collaboration across technology readiness levels include machining research where experimental data is recorded at AMRC and analysed within the department.
The structural testing facilities are located in the Lea Laboratory. These include a range of loading capacity from 5-250kN electro-mechanical and servo-hydraulic test frames for axial, bi-axial and multiaxial (Tension-Torsion-Compression) testing. Our testing facilities are capable of running standard and highly customised material and structural loading tests.
Micromechanical testing with damage characterisation is carried out inside scanning electron microscopes in the Sorby Centre and inside an X-ray micro-Computed Tomography microscope in the ºù«Ӱҵ Tomography Centre.